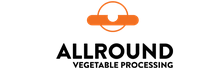
Allround Vegetable Processing: Engineering Innovation In Vegetable Processing For Indian Market & Neighbouring Country
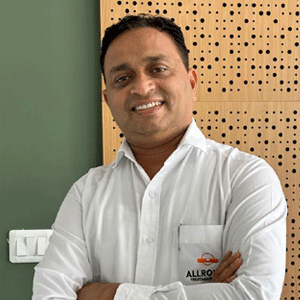
Mohd. Faruk , Head - Sales
India’s food-processing machinery sector is accelerating as rising incomes, urban snacking habits, and government schemes like PM-FME push processors to add capacity, lifting equipment demand toward ₹38,000 crore by 2030. Growth is spurred by horticulture output that now surpasses cereals, creating year-round need for washing, peeling, grading, and IQF lines. Yet 20-25 percent of perishables still spoil before value-addition because SME plants rely on ageing, labour-intensive gear and patchy cold chains, while global retailers demand traceable, hygienic processing compliant with FSMA and FSSAI norms. Into this gap steps Allround Vegetable Processing. A Dutch company offering identical quality in both Holland and Indian factories, Allround Vegetable Processing provides modular post-harvest machinery for potatoes, carrots, and onions, cleaning, grading, washing, handling and storage. With a pick-your-capacity model, it reduces waste and labour, boosts yields, and enables affordable modernization, solidifying its position as a segment leader.
Integrated Manufacturing
Supplying six or seven of every ten potato preprocessing lines installed across India, the company stands as the segment’s dominant equipment provider. Its portfolio covers the full receiving section, receiving hoppers, cleaners, graders, short-term storage, washers, and destoners, ensuring defect-free tubers reach the peeler and maximizing upstream yield. Complementing this machinery, the firm engineers specialised cold-storage facilities designed for snack-grade potatoes & others. Central to these stores is the e-Gate interface, an IoT platform that allows remote control of temperature, CO₂, and humidity through a mobile application. The system maintains potatoes for seven to twelve months without sugar developing & with very less weight loss.
"Our e-Gate platform proactively monitors cold storage conditions, instantly alerting technicians to any deviations, be it temperature, humidity, or CO₂ imbalances, enabling swift corrective actions. In case of component failures, our system precisely identifies the affected part and time, minimizing downtime and preserving product quality”, speaks Mohd. Faruk, Head (Sales), Allround Vegetable Processing. Recent R&D has extended this data layer to smart hoppers & storage hoppers, which hold tubers up to 24 hours without quality loss, and integrated load–unload controls sync with e-Gate to log throughput volumes and cycle times. Together, these innovations pair granular environmental telemetry with responsive automation, giving processors a live dashboard of product health and equipment performance from intake to line feed.
Expansion Roadmap
Allround Vegetable Processing has firmly established itself as a leader in India’s vegetable-pre processing equipment sector by focusing on innovation, reliability, and customer-centric solutions. Four levers set the company apart in this competitive aren. The firm consistently brings the latest European technologies to the Indian market, ensuring timely access to cutting-edge innovations. First, its fully integrated manufacturing plant in Ambala shortens lead times and slashes import duties, making machines cost competitive. Second, a nationwide service backbone, with head offices in Ahmedabad and Mumbai plus field Engineers and technicians, delivers rapid after-sales support. Third, in-house production of most of the component keeps maintenance low and ensures critical spares are always available, and clients can order parts on demand instead of carrying costly inventories. Finally, customer retention exceeds a decade with marquee processors because the firm routinely custom-engineers’ solutions, often at no extra charge, through a dedicated R&D cell and state-of-the-art fabrication facilities.
The company’s roadmap centres on relentless R&D and capacity expansion. A second Indian manufacturing plant, scheduled for inauguration within the next two months, will double fabrication throughput and shorten delivery cycles. Parallel to this brick-and-mortar growth, engineers are embedding artificial intelligence into the optical-sorting line, using advanced vision algorithms to boost accuracy and cut labour dependence. Continuous experimentation with AI-driven predictive maintenance is also under way, enabling machines to flag wear well before breakdown. Each innovation is tested against India’s unique operating conditions, so new releases remain rugged yet affordable. Looking ahead, management pledges to introduce at least one breakthrough feature every year, ensuring processors stay ahead of evolving quality norms while enjoying the same trouble-free reliability that has become the firm’s hallmark.
Integrated Manufacturing
Supplying six or seven of every ten potato preprocessing lines installed across India, the company stands as the segment’s dominant equipment provider. Its portfolio covers the full receiving section, receiving hoppers, cleaners, graders, short-term storage, washers, and destoners, ensuring defect-free tubers reach the peeler and maximizing upstream yield. Complementing this machinery, the firm engineers specialised cold-storage facilities designed for snack-grade potatoes & others. Central to these stores is the e-Gate interface, an IoT platform that allows remote control of temperature, CO₂, and humidity through a mobile application. The system maintains potatoes for seven to twelve months without sugar developing & with very less weight loss.
"Our e-Gate platform proactively monitors cold storage conditions, instantly alerting technicians to any deviations, be it temperature, humidity, or CO₂ imbalances, enabling swift corrective actions. In case of component failures, our system precisely identifies the affected part and time, minimizing downtime and preserving product quality”, speaks Mohd. Faruk, Head (Sales), Allround Vegetable Processing. Recent R&D has extended this data layer to smart hoppers & storage hoppers, which hold tubers up to 24 hours without quality loss, and integrated load–unload controls sync with e-Gate to log throughput volumes and cycle times. Together, these innovations pair granular environmental telemetry with responsive automation, giving processors a live dashboard of product health and equipment performance from intake to line feed.
Expansion Roadmap
Allround Vegetable Processing has firmly established itself as a leader in India’s vegetable-pre processing equipment sector by focusing on innovation, reliability, and customer-centric solutions. Four levers set the company apart in this competitive aren. The firm consistently brings the latest European technologies to the Indian market, ensuring timely access to cutting-edge innovations. First, its fully integrated manufacturing plant in Ambala shortens lead times and slashes import duties, making machines cost competitive. Second, a nationwide service backbone, with head offices in Ahmedabad and Mumbai plus field Engineers and technicians, delivers rapid after-sales support. Third, in-house production of most of the component keeps maintenance low and ensures critical spares are always available, and clients can order parts on demand instead of carrying costly inventories. Finally, customer retention exceeds a decade with marquee processors because the firm routinely custom-engineers’ solutions, often at no extra charge, through a dedicated R&D cell and state-of-the-art fabrication facilities.
The company’s roadmap centres on relentless R&D and capacity expansion. A second Indian manufacturing plant, scheduled for inauguration within the next two months, will double fabrication throughput and shorten delivery cycles. Parallel to this brick-and-mortar growth, engineers are embedding artificial intelligence into the optical-sorting line, using advanced vision algorithms to boost accuracy and cut labour dependence. Continuous experimentation with AI-driven predictive maintenance is also under way, enabling machines to flag wear well before breakdown. Each innovation is tested against India’s unique operating conditions, so new releases remain rugged yet affordable. Looking ahead, management pledges to introduce at least one breakthrough feature every year, ensuring processors stay ahead of evolving quality norms while enjoying the same trouble-free reliability that has become the firm’s hallmark.
🍪 Do you like Cookies?
We use cookies to ensure you get the best experience on our website. Read more...